Intertek's expertise in analysing the remaining useful life of tubes in superheaters and reheaters can help power plant operators avoid costly tube failures and downtime.
Tube failure is one of the leading causes of forced outages in power plants. One of the key ways of preventing failure is to predict the remaining useful life of tubes. By gaining an accurate assessment of the predicted lifespan of the tube, power plant operators have the necessary information to make decisions on prioritising future inspections, and whether to run, repair or replace tubes.
How we analyse the remaining useful life of tubes:
The lifespan of a superheater or reheater tube is affected by time, temperature and stress.
To measure the remaining useful life of the tube, information on the steam pressure, original and present wall thicknesses and the tube’s outside diameter (OD) is used to calculate the stress history of the tube. The steamside scale thickness is used to gauge the effective temperature history of the tube.
The stress history and the effective temperature history are compared to the creep rupture material of the specified tube material. From this information, the remaining useful life of the tube can be calculated – as well as the temperature profiles across the boiler.
Hot spots and wastage patterns can also be identified.
Using leading technology:
Intertek has extensive experience using their remaining useful life analysis system – TubeAlertSM and TubeTechSM – to predict the lifespan of tubes and providing Total Quality Assurance. The system measures the oxide and wall thickness of the tube during an on-site non-destructive test and this is used to calculate the remaining useful life.
Intertek developed the oxide measuring technology in 1981 and it is now used as the standard throughout the world. The Electric Power Research Institute (EPRI) of the United States has endorsed the technology and Intertek continues to improve and refine the oxide measuring technology.
A-Z List of Power Generation Services
Solutions
Asset Integrity Management (AIM) Services
Our Asset Integrity Management (AIM) Services such as engineering, inspection, and surveying help owners and operators gain maximum asset value while minimizing risk and improving safety.
Oil and Gas Industry Solutions
Upstream, Midstream and Downstream, get support for your production, engineering, training, quality and inspection needs.
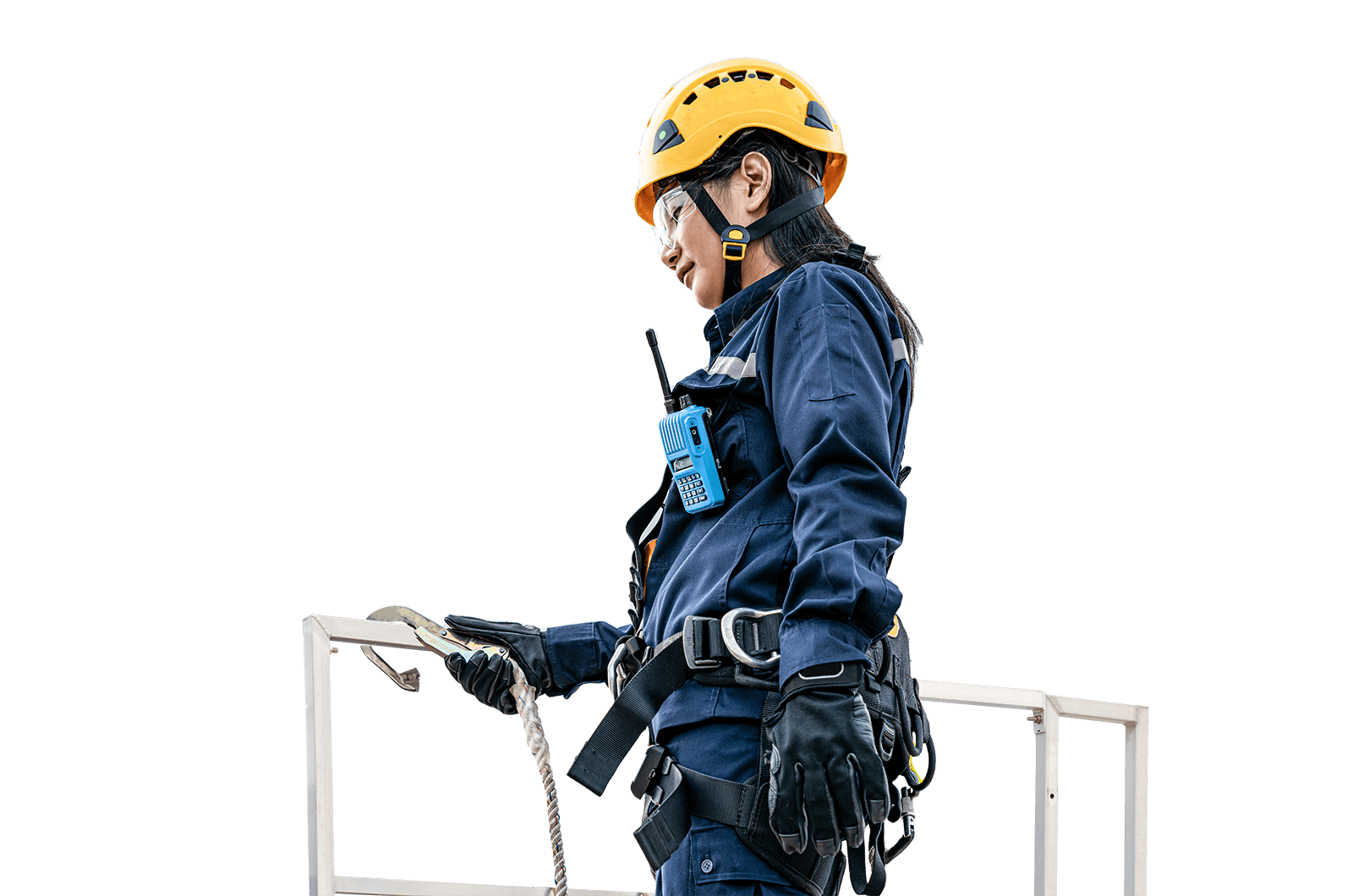