Expert testing for optical properties of polymers, including haze, gloss, colour, clarity and more, bringing you the insight you need to accelerate the development of new materials and optimise quality and consistency in production
Optical properties of polymers, such as gloss, transparency, clarity, haze, colour, surface aspect and refractive index, are closely linked to our perception of a plastic product’s quality and visual performance. Polymer optical properties testing will bring you the insight you need to accelerate the development of a novel material or to optimise or troubleshoot production.
Optical properties depend on the specific polymer or copolymer material, the formulation (colourants, fillers, plasticisers and other additives) and the crystallinity of the materials. However, mechanical and chemical degradation or ageing processes and the mechanical conditions and/or temperature treatments applied during processing influence the optical properties of polymers and polymer formulations. Any negative impact on a polymer’s optical properties - such as ageing - can affect the product’s lifetime, even whilst the functional or mechanical properties still meet specifications.
Innovators know that a product's aesthetics must be maintained throughout its packaging, transport, and storage. This is especially true in the automotive industry, where a consumer’s perception of ‘glossy’, strong surface features is inextricably linked to the product's 'value'. During production, various steps, such as colouration, heat treatment, and mechanical processing, can affect optical properties.
From our independent perspective, we expertly analyse a range of optical properties, delivering accurate information that helps achieve the desired aesthetics during development, production, or end-use application. Through our testing programs—including fundamental tests such as gloss, haze, birefringence, and Ultra-Violet and Visible (UV/VIS) light absorption and transmission—Intertek can help you optimise production to achieve optical property specifications.
Refractive Index
The refractive index and light transmission of transparent materials for example, those use in lenses, optical fibres, large screen displays or coatings, are relatively straightforward to measure accurately. Intertek’s polymer laboratories use refractive index (ASTM D542) as a diagnostic tool to help understand the critical stress in a system or the resulting impact of additives or heat treatments (such as cross linking, or annealing) have on the material. We also provide ultra-violet and visible (UV/VIS) light absorption and transmission measurements.
Birefringence
The polymer refractive index varies with orientation of the polymer chains on a molecular level; our polymer scientists use polarized light to achieve birefringence effects which can be used to quantify the stress in a transparent plastic.
Clarity and Light Transmission
To address polymer transparency, we measure the degree of light transmission using ASTM D1003 (Standard Test Method for Haze and Luminous Transmittance of Transparent Plastics) and this test method is used to evaluate light transmission and scattering of transparent plastics for a defined specimen thickness. For optical clarity of polymers we use the BYK method.
Whiteness Color Measurement and Analysis
Most polymers are typically grey or yellow coloured. White fillers or other optically active additives colour additives can help to make the appearance more suited to application. Our experts use whiteness colour or colour measurement to measure colour in terms of L*a*b* colour space using Colorimetry as per Part 4: CIE 1976 L*a*b* colour space (ISO/CIE 11664). We routinely evaluate color properties of polymers or color change due to exposure to adverse conditions or to help match parts molded from different materials or assess color changes due to surface texture or molding or processing.
Yellowness Index
Yellowness Index is a number calculated from spectrophotometric data that describes the change in color of a test sample from clear or white to yellow. Intertek uses the yellowness index test to evaluate color changes in a material caused by real or simulated outdoor exposure.
Specular Gloss
Gloss is the capacity of the polymer surface to reflect light in a given direction. Intertek provides testing for gloss (ASTM D2457) on a range of sample types and sizes, at different incidence angles delivering comparative data between similar samples thus supporting development and end use performance testing.
Haze
Haze is an optical effect caused by light scattering within a transparent polymer resulting in a cloudy or milky appearance. Our polymer scientists test for haze in accordance with ASTM D1003 using spectrophotometer techniques to investigate a range of issues which result in haze as a symptom such as weathering, during product and process development.
Our polymer scientists understand that the optical properties of polymers are closely related to the chemical microstructure, thermal and physical properties of these materials, and as such, we provide comprehensive expertise that covers chemical, physical, mechanical and thermal testing. Our industry application experts take you beyond the test result, using their experience and knowledge to provide the guidance you need to achieve improvement of a material's optical properties and maintain consistent appearance and quality.
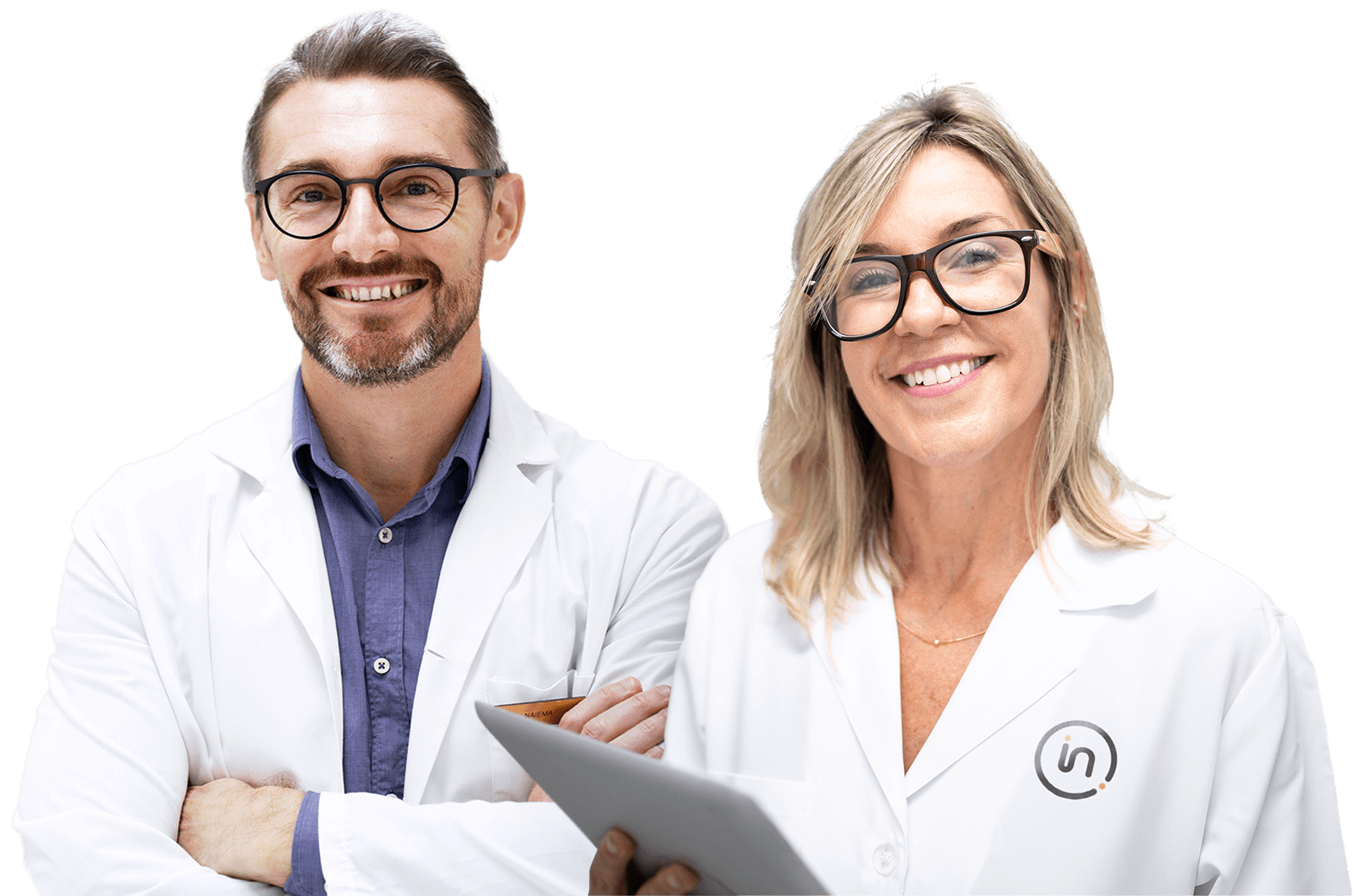