Intertek CAPCIS perform sulphide stress corrosion and hydrogen induced cracking tests in accordance with standards such as EFC 16 & 17, NACE TM0177-2005 and TM0284-2003
Sour service testing offers a detailed insight into the endurance thresholds of the materials used across a wide variety of industries, including oil and gas.
The correct selection of materials for operation in H2S-contaminated atmospheres, or sour environments, is essential to minimise risks and assure cost-effectiveness.
Additionally, sour service testing enables the qualification of materials for specific environmental limits and illustrates the compliance of products to suppliers’ acceptance criteria.
Prior to their selection for service, materials need to be assessed against likely corrosion failure mechanisms through sour service testing.
To assure accuracy, testing methods need to be tailored to the anticipated mechanisms, which can include sulfide stress cracking, chloride stress corrosion cracking and galvanically induced hydrogen stress cracking.
For high-quality, reliable sour service testing and consultancy, you need an experienced partner like Intertek CAPCIS with decades of knowledge, cutting-edge equipment and world-class expertise.
Whether high-pressure, high-temperature or dynamic testing is required, we possess the facilities to handle virtually any production scenario. We can simulate pressures up to 1,300 bar and temperatures in excess of 300C and operate 18 test frames, nominally 10-100 kN capacity.
Our Total Quality Assurance experience in sour service testing and high-pressure experiments has facilitated the development of a unique high-pressure fatigue testing capability of up to 70 bar.
Assessments of general and localised corrosion can be undertaken, as well as electrochemical measurements in dynamic and static testing conditions.
The testing we conduct complies with recognised industry standards, namely EFC 16 and 17, NACE TM0177, NACE TM0284 and NACE TM0198. This allows the fitness-for-service qualification of corrosion-resistant alloys and steels in accordance with ISO 15156 in a wide range of sour service environments.
Additionally, we hold UKAS accreditation (Laboratory 8603) for methods:
- NACE TM0177 method B-2016 Sulphide Stress Corrosion Cracking (SSCC) – Four Point Bend Test
- NACE TM0284-2016 Hydrogen Induced Cracking (HIC)
Conducting sour service testing for over 50 years, we have built long-standing relationships with a range of clients, from international oil and gas companies to flexible pipe manufacturers and steel producers.
With over 300 laboratories across 100 countries, our global reach enables us to provide you with vital services on a worldwide scale.
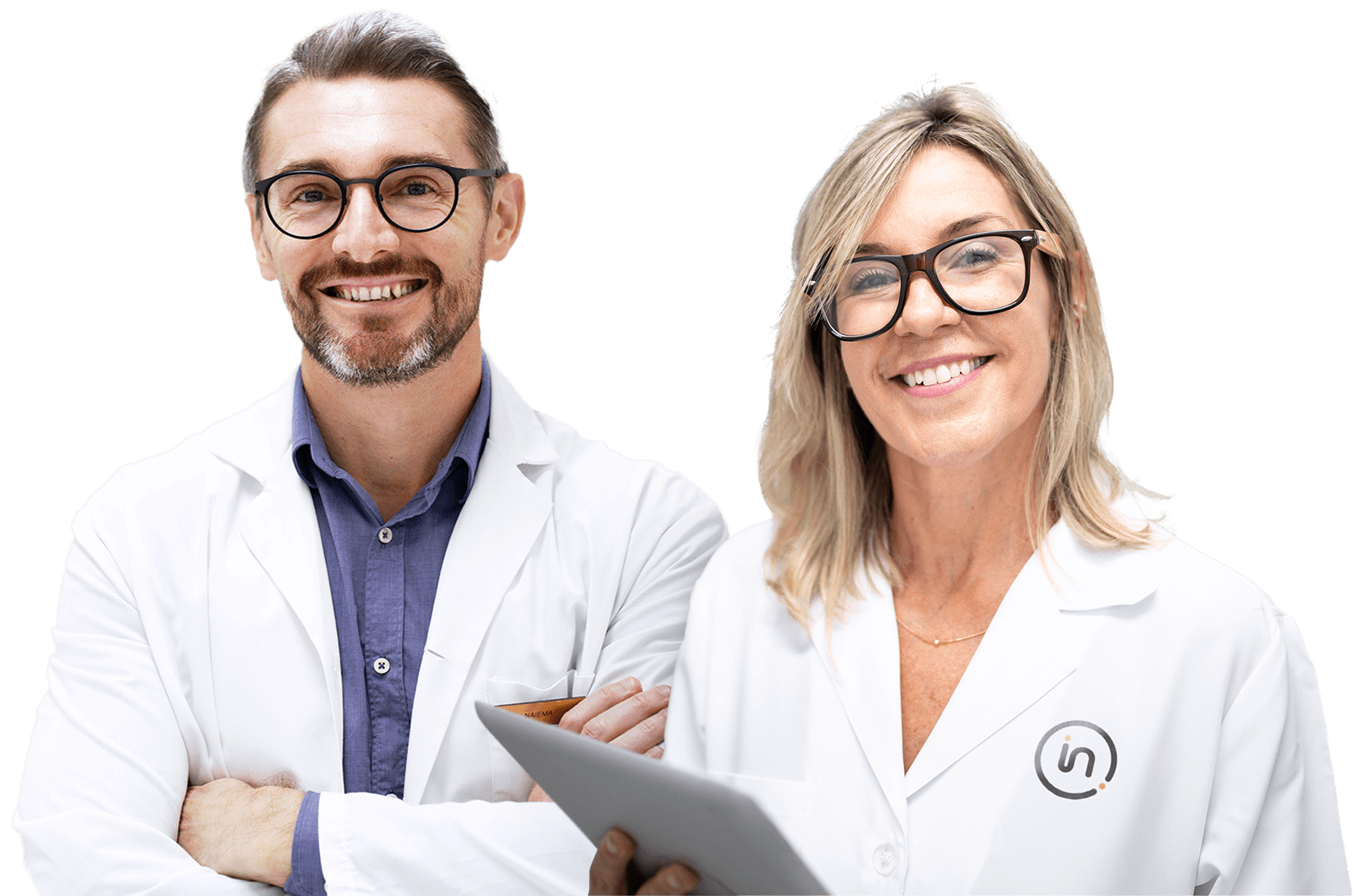