Understanding Defects and Delivering Solutions Via Failure Analysis
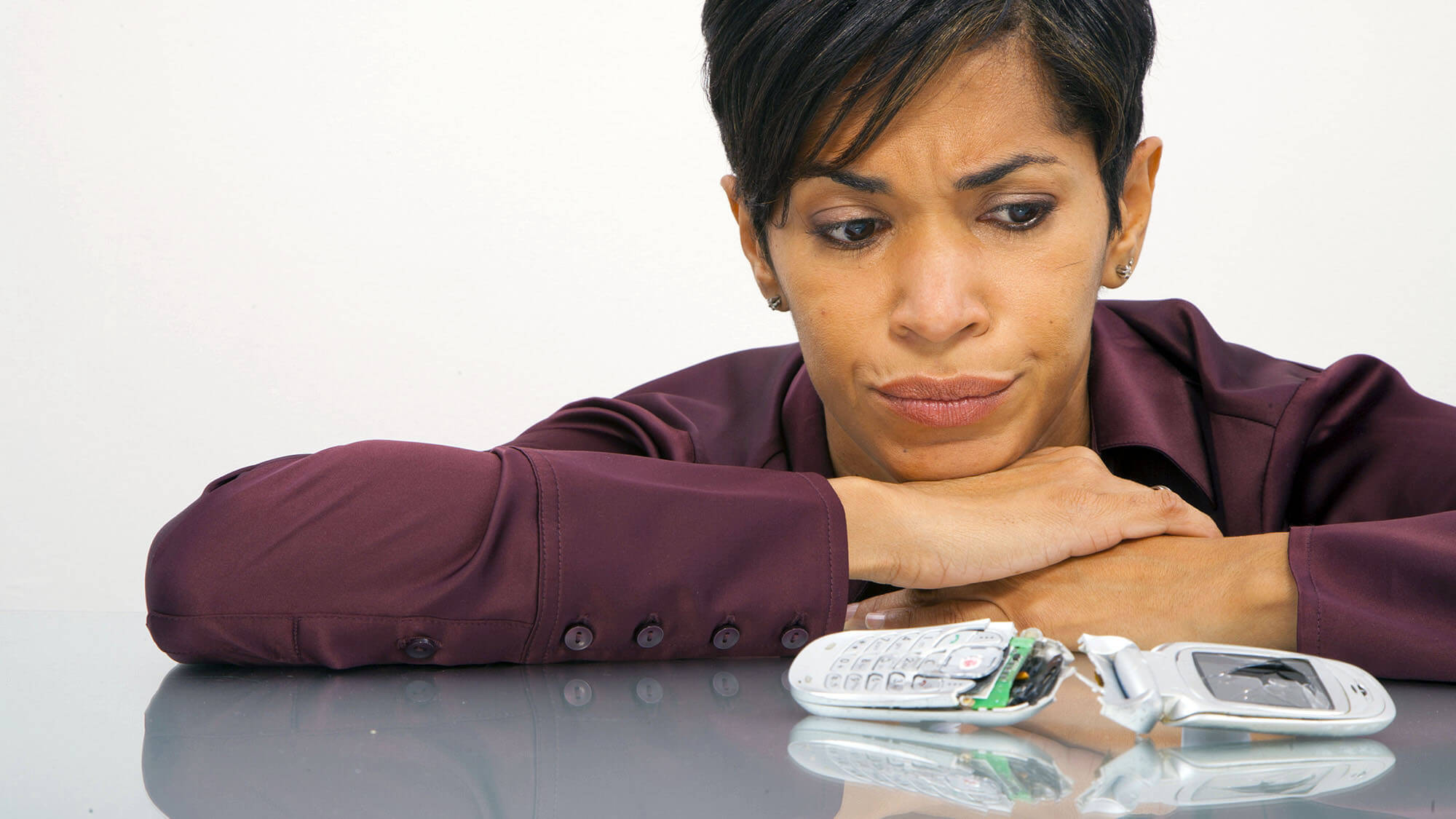
01 Apr 2025
Leveraging these Incidents as Valuable Learning Opportunities to Inform Better Design and Manufacturing Practices
Failure analysis is an essential process in engineering, manufacturing, and product development, as it helps to ensure that any defects and malfunctions are identified, understood and used to prevent them from occurring in future applications. The failure analysis process follows a stepwise approach, leveraging advanced tools and techniques to diagnose failures.
A failure is defined as a product or component behaving in a way that deviates from its design intent, leading to a performance shortfall. Failures can and do occur across virtually every type of industry, including automotive, aerospace, medical devices, consumer products, architecture, electronics, and even agriculture. However, through meticulous failure analysis, these incidents can become valuable learning opportunities, informing better design and manufacturing practices.
Case Studies: Lessons from Failure
Tackling Knit Line Defects in Plastic Moldings for Automotive Components
One example that Intertek helped identify via failure analysis came from the automotive industry where materials, such as metal and polymers, face extreme environmental conditions ranging from bitter cold to incredible heat. This particular case involved nylon clips reinforced with short glass fibers that exhibited a knit line failure near a cavity. The glass fibers in this area were mostly oriented parallel to the material flow instead of being randomly dispersed in the matrix. This reduced the strength of the matrix when a force was applied to this area and resulted in a fracture. Through microscopic inspection, Intertek analysts confirmed that the defect was caused by improper mold and part design, allowing the client to make adjustments to prevent future failures.
Environmental Stress Cracking in Trailer Lamps
Another investigation focused on trailer lamps made from polycarbonate, which developed fractures after a year of field use. Initial visual and microscopic inspections identified stress fractures concentrated at corners. Chemical analysis revealed that detergents used during routine cleaning had induced environmental stress cracking. This information enabled the manufacturer to reassess material selection and improve chemical resistance for future designs.
Lithium-Ion Battery Capacity Fade
Battery failures are another critical area of failure analysis, particularly with lithium-ion cells. In one case, a pouch cell exhibited capacity fade, leading to performance issues. Analysts performed non-destructive X-ray and CT scans to examine internal structures before opening the cell. Further chemical analysis verified that the electrolyte composition met specifications, ruling out contamination. The investigation concluded that the issue stemmed from testing conditions rather than a manufacturing defect, emphasizing the importance of comprehensive validation.
Dendritic Growth in PCBs
Printed circuit boards (PCBs) are also subject to failures that require detailed analysis. In one case, circuit boards exhibited dendritic growth, a conductive residue forming on the PCB surface that can lead to short circuits. Using scanning electron microscopy (SEM) and energy-dispersive spectroscopy (EDS), analysts confirmed the presence of tin dendrites, which formed due to improper handling prior to environmental exposure. The analysis helped the client refine cleaning protocols and improve board reliability.
Gray Speckles on Eggshells
Failure analysis can even extend beyond conventional industrial applications and manufactured products. One very unique case we were asked to assist with involved mysterious gray speckles appearing on eggshells and darkened chicken feet. Investigators traced the issue to a recent change in the feed used in the coops, which was recently switched to galvanized steel. Chemical analysis confirmed zinc contamination in the chicken feed, which was then transferred to the eggshells. Identifying the root cause enabled the client to replace the fencing, eliminating the defect.
The Methodology Behind Failure Analysis
The failure analysis process follows a structured approach, starting with initial inspection and background information gathering. Analysts use various microscopy techniques, from optical to SEM, for visual documentation. Non-destructive methods like X-ray and CT scanning help assess internal components before destructive testing. Material characterization, including spectroscopy and thermal analysis, provides insights into composition and physical properties. Performance testing replicates failure conditions, allowing investigators to determine the exact mechanisms at play.
Different tools are deployed based on the nature of the failure. SEM-EDS is particularly useful for studying fracture surfaces and identifying contaminants. Optical microscopy aids in coating thickness measurements and substrate analysis. Digital microscopes provide depth-of-field advantages for inspecting surface finishes. Infrared spectroscopy (FTIR) is key for polymer identification, while gas chromatography-mass spectrometry (GC-MS) helps detect organic additives in materials.
Beyond Diagnosis
Understanding why a product failed is only part of the objective. Failure analysis also provides valuable data for improving manufacturing processes and material selection. Identifying trends in failures ensures that defects will not persist in future production runs. By partnering with a third-party lab, such as Intertek, companies gain objective insights into failure causes which can help resolve disputes between manufacturers and suppliers.
Failure analysis is not only about diagnosing the present failure but also about preventing future occurrences. With rigorous investigation techniques, engineers can refine product designs, enhance material performance, and ensure higher reliability across industries.