Wired for Success: The Role of Quality Assurance in Electrical Product Manufacturing
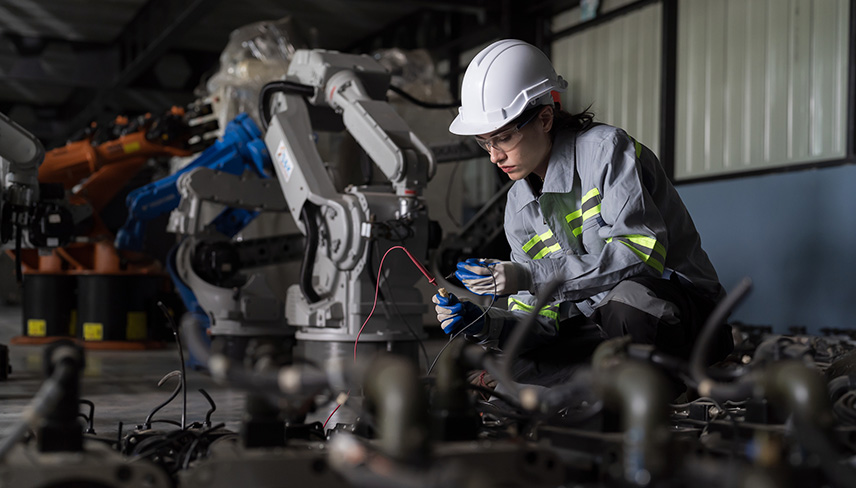
26 Mar 2024
A look at some key components to incorporate into your QA program
In today's consumer landscape, purchasing decisions extend beyond aesthetics and features; consumers prioritize safety, sustainability, and social responsibility. For electrical product manufacturers, implementing a robust Quality Assurance (QA) program is not just a choice—it's a necessity. This blog post explores the multifaceted importance of QA programs in ensuring the safety, reliability, and overall quality of electrical products.
Safety Testing and Certification
QA programs include rigorous safety testing and certification processes, addressing compliance with various regulatory and industry standards. These measures ensure that products adhere to safety guidelines such as those set by the Occupational Safety and Health Administration (OSHA) in the United States.
Electromagnetic Compatibility (EMC) Testing
EMC testing assesses an electrical product's ability to function in its intended electromagnetic environment without interfering with other devices. Compliance with relevant regulatory and industry standards is crucial for seamless and interference-free operation.
Energy Efficiency and Sustainability Testing
QA programs evaluate energy efficiency, carbon footprint, and environmental impact throughout a product's lifecycle. This testing ensures products meet sustainability standards, reducing their overall environmental footprint.
Hazardous Locations Certification
For electrical products intended for use in potentially explosive environments, QA programs include testing and certification processes to guarantee safety in hazardous locations, where flammable materials may be present.
Fire/Flammability Testing:
To prevent fire hazards, manufacturers conduct fire and flammability testing to assess the safety of their products, meeting necessary safety requirements.
Accelerated Stress Testing
QA programs employ accelerated stress testing to simulate long-term product usage, identifying potential failures and design flaws before market release. This proactive approach helps manufacturers rectify issues early in the development process.
Cybersecurity Testing
Given the rise of cyber threats, QA programs incorporate cybersecurity testing to identify vulnerabilities in a product's software and hardware systems, protecting against hacking and data breaches.
Usability and Interoperability Testing
Usability and interoperability testing are integral components of QA programs, ensuring products meet user needs and seamlessly integrate with other systems within their intended environment.
Corporate Social Responsibility (CSR)
Beyond performance and safety, QA extends to corporate social responsibility. Manufacturers must uphold ethical and sustainable practices, aligning with consumer expectations for socially responsible products.
Supply Chain Validation
QA programs include supply chain validation to ensure high-quality materials and components, meeting stringent standards and regulations throughout the manufacturing process.
Quality Management Systems (QMS) and Six Sigma
Implementing a QMS is crucial for continuous improvement and risk management, identifying and addressing quality issues early in the production process. Six Sigma, a statistical analysis-based methodology, minimizes defects and errors, enhancing overall product quality.
In conclusion, a comprehensive QA program is indispensable for electrical product manufacturers. It not only ensures compliance with safety standards but also addresses environmental impact, cybersecurity threats, and social responsibility. By prioritizing quality at every stage, manufacturers can deliver products that meet consumer expectations, withstand the test of time, and contribute to a safer and more sustainable future. For a more in-depth look at these key aspects of a sound Quality Assurance program, download our white paper: Elements of a Successful Quality Assurance Program.
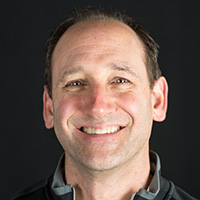
Derek Silva,
Vice President, Marketing, North America
With 30 years of marketing experience, Derek Silva leads Intertek's North America Products Marketing team to create awareness of the company's safety and quality assurance solutions for manufacturers, retailers, traders, governments, consumers, and other organizations. Since joining Intertek 20 years ago, Derek has held various marketing and communications positions supporting a number of business lines through the development and execution of advertising, digital and social media campaigns, trade show participation, web strategy, corporate branding, sales enablement programs, and internal communications. His experience spans a wide range of industry verticals, including aerospace, automotive, IT/telecom, HVAC, industrial, building materials, renewable energy, medical, fire/security, lighting, and more.