5 Steps to Watch out before and after Lubricant Oil Sampling
27 Apr 2021
Proper sampling generates accurate analysis and effective action plans
Lubricant (or oil) analysis is proven over the years to provide an accurate picture of the condition of a piece of equipment. That being said, the sampling must be performed with extreme care in order to provide the best representative sample for analysis. This in turn will yield an accurate Analysis Report, which will then be used by the maintenance team to create effective oil condition-based action plans.
On the other hand, incorrect sampling will generate an inaccurate analysis and consequently an ineffective action plan. That's why it is imperative for the sampling technician to take every precautionary measure and adhere to the below steps in order to avoid external contaminants and false positives, which mostly occur during the sampling process.
BEFORE
- Consider sampling from operational equipment
The best representative sample is obtained when the sampling is performed from a live zone while the equipment is in operation. Bends, elbows, before filter are some of the preferred locations to attain a perfect representative sample for analysis. - Sampling from an idle equipment
Avoid sampling from idle equipment. However, if the sample can only be taken from an equipment in non-operational condition, it is always advisable to perform sampling within 15 mins after the equipment was made idle. This assists in preventing False Positives and False Negatives during sampling. - Avoid sampling from the drain.
Samples must be drawn from recommended sampling ports/valves. Since the majority of the dead additives, sediment and water gets separated from the oil in circulation and will settle down at the bottom, there is a high risk that this will get into the sample drawn from the drain, which can pave the way for False Positives. - Use appropriate sampling kits
Sampling must be performed using the recommended accessories for each equipment (vampire sampling pump, oil plug valve, sampling tube, sampling bottles, tube cutter) in order to prevent undesirable contaminant ingress to both the oil sample and most importantly the equipment. - Maintaining a clean sampling port is paramount
Prior to sampling, ensure the area near sampling port is tidy and dry. This will prevent contaminants from finding their way to the equipment during sampling process.
AFTER
- Seal the sample bottle
Once the required sample quantity is drawn, remove the sample bottle from the vampire pump and seal the sample bottle tightly to prevent external contamination and oil spillage during transit to the laboratory. - Close the sampling port
The sampling port/valve must be immediately closed to avoid contaminant ingress to the system. The longer the sampling ports are left open, the higher the chances of the system getting contaminated. - Sampling with a vampire pump
As the vampire pump is removed from the sample bottle, cut the sampling tube above the vampire pump with a suitable tube cutter. Hold the pump in a horizontal position and pull the sampling tube downwards. This will assist in preventing pump contamination by the oil sampled. - Augment your data density
All the available equipment details are to be included in sample job card. Availability of substantial data helps the Diagnostician to make conclusive and precise diagnosis on oil condition, which subsequently assists the maintenance team to implement condition-based maintenance. - Submission of oil sample
Ensure oil sample reaches the nearest Intertek OCM laboratory for detailed analysis.
For further details, feel free to contact your nearby Intertek office.
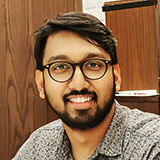
Kiran K,
Lubricant Diagnostic Engineer
Kiran K is a Lubricant Diagnostic Engineer with over six years of experience in the field of Oil Condition Monitoring. Being a Mechanical Engineer and a ICML MLA II certified professional, he has vast expertise on machinery Lubricants and Tribology. He assists regulatory bodies to set benchmark test requirements for lubricating products and provides technical expertise to asset management team on machinery health based on oil condition, which assists them to prolong useful life of machinery in an ever better way.