Digitization of Asset Integrity Management (AIM)
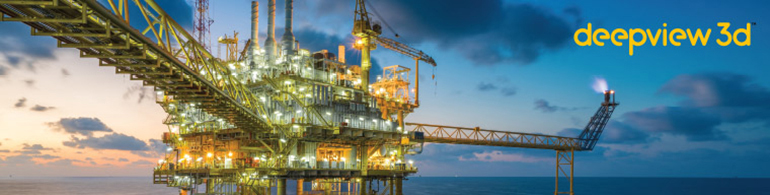
12 Nov 2019
Implementing a Digital Transformation
Equipment and technology have been evolving at a very fast pace in the last couple of decades to satisfy specific purposes in our lives. Physical asset management strategies have evolved as well, but mostly because of the need to match new technology demands such as performance optimization, life cycle management, and the cost of reliability.
With the rise of modern business digitization, stakeholders, engineers, and technicians are recreating, or at least trying to accommodate, current processes for the arrival of new technology and aggressive implementation plans. The main objectives of digitizing asset management are to (1) reduce human intervention for high-cost decision making; (2) minimize personnel interactions in the field for critical activities; and (3) achieve greater asset reliability through the utilization of advanced automation, simulations, and continuous access to real-time data. However, technology planning and implementation that matches business strategies can lead to misconceptions with costly repercussions. In many cases, the result is the inefficient copying of external models, even when those models are not applicable to the company's reality.
Industries such as aerospace, automotive, and other modern manufacturing sectors have long been introducing digitized asset management. Today these companies are raising the standard, promoting "proactive life cycle management" and associated technologies with real-time operations and remote or artificial decision management. Oil and Gas, Energy, and Mining sectors are trying to catch up and have invested efforts and capital to re-engineer their business processes to support technologies that provide competitive advantages in production flow, quality, and reliability. Service providers are offering solutions such as virtual reality, digital twins, IIoT, big data, and cloud computing, making the selection process complicated and expensive at the same time. Many suppliers, however, often fail in understanding the client's current state and constrains making technology an additional problem instead of a solution.
Advanced Digital Integrity Solutions (ADIS) is Intertek's AIM approach to implementing digital transformation efforts using new and advanced technology in the areas of Asset Management, Life Cycle Management, Risk Management, Assurance, and Reliability. Our vision is to provide innovative digital strategies and technologies that will help our clients operate efficiently in a digital world, which will aid in making their operations safer, cost effective, and environmentally friendly. ADIS is a digital AIM program that combines design, maintenance, inspection, process, operation, and management activities beyond traditional methods by incorporating cutting edge technologies such as 3D laser scanning, metrology, NDE, 3D modelling, Point Cloud and Asset Management Software, UAV Surveying, interconnected worker, and augmented reality.
We recognize that new technology and systems do not achieve goals by themselves. ADIS ensures participation and integration of the entire production and operations structure during the conceptualization, design, and validation processes of digital transformation. We understand the applicability of the solution: analyzing the gap of the existing resources versus the upcoming, eliminating resistance, and creating trust among the operating groups. All of these play crucial roles toward success while planning and designing the Digitization of Asset Integrity Management.
Figure 1. The ADIS Structure represents key practices and strategies that must be implemented to assure Total Quality and Reliability.
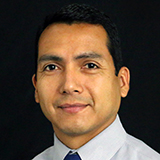
Rene Canales,
Sr. Reliability & Systems Engineer, Digital Solutions Specialist
Mr. Canales is a Reliability and Systems Engineer with more than 10 years of experience in the Oil and Gas, Energy, and Aerospace industries. In addition to his background of successful experience in reliability, he has spent years in digital asset management and real time operations of deep-water exploration, Blowout Preventers (BOP), and NASA Space Operations. His professional experience has been successfully attained in the areas of Asset Integrity Management (AIM), Total Productive Maintenance (TPM), Reliability Centered Maintenance (RCM), Root Cause Failure Analysis (RCFA), Failure Mode and Effects Analysis (FMEA), and Real-Time Data Analytics.