Microscopy expertise aiding process engineers and scientists involved in the design, production, testing of medical devices and healthcare materials
Intertek's microscopy of medical devices expert teams deliver valuable information to help process the work of engineers and scientists involved in the design, production and testing of medical devices such as catheters, stents, coils, endoscopes, and other healthcare materials such as implants and disinfectants.
Microscopy of medical devices is a specialist and demanding field, demanding long and involved industry experience. Our microscopy teams have a long involvement in the fields of polymer science, materials characterization and microanalysis, with the ability to successfully interpret and explain all aspects of microstructure/ product-property relationships in terms of fundamental principles which will help process-engineers improve the performance of the devices under their stewardship.
Intertek understands polymer science, adhesion and bonding, which helps to deformulate raw materials and understand metallurgical processes such as fracture and corrosion.
Intertek's medical device production problem solving capability has led to significant improvements in client product yield, and our materials science consultancy has led to improvements in product design. We are able to identify "at fault" raw material suppliers and facilitate the resolution of end user complaints.
Medical device microscopy requests:
- Deformulation of raw materials and assessment of raw material manufacturing processes
- Adhesion and bonding investigations
- Evaluation of moulded-in stresses and strains
- Weld integrity issues such as surface contamination and weld homogeneity
- Microstructure – product property relationships
- End-user complaint investigation and validation
- Failure analysis of polymers, coatings and metals
- Product contamination and defect assessment
- Polymer science consultancy
Medical device microscopy successes:
- Increased production yields (less rework/scrap)
- Improved risk management through lower failure rates on product testing
- Optimisation of raw materials through improved specifications
- Development time reduced and re-validation prevented
- Improved extrusion quality impacting on down-stream sub-assembly processes
- Improvement of mechanical properties
- Previously unknown regulatory issues identified
- "At fault" suppliers (and customers) identified
*Intertek Assurance does not provide consulting services for management systems certification. Any consulting activities provided by Intertek are separated and independent from testing and certification activities.
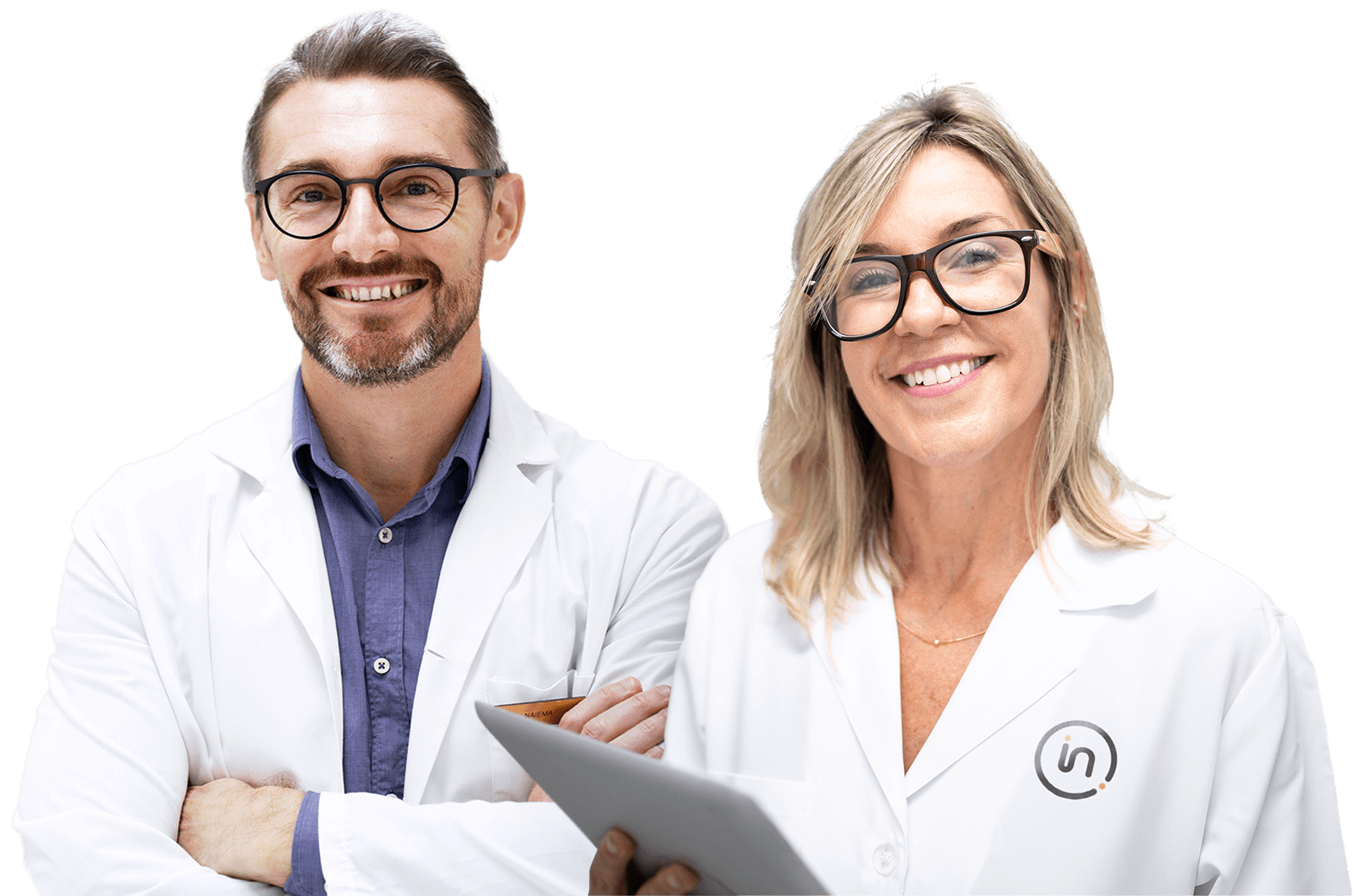